It is carnival season once again, so doughnuts are now back on the scene in Germany. Different flavors and fillings, e.g. strawberry jam, eggnog cream or chocolate pudding make the hearts of those with a sweet tooth beat faster. The large bakeries face the challenge of meeting the high demand. Automatic production lines make it possible to supply these diverse fillings, which are freshly prepared in boilers, to the pastry filling plant in a hygienic and highly efficient manner.
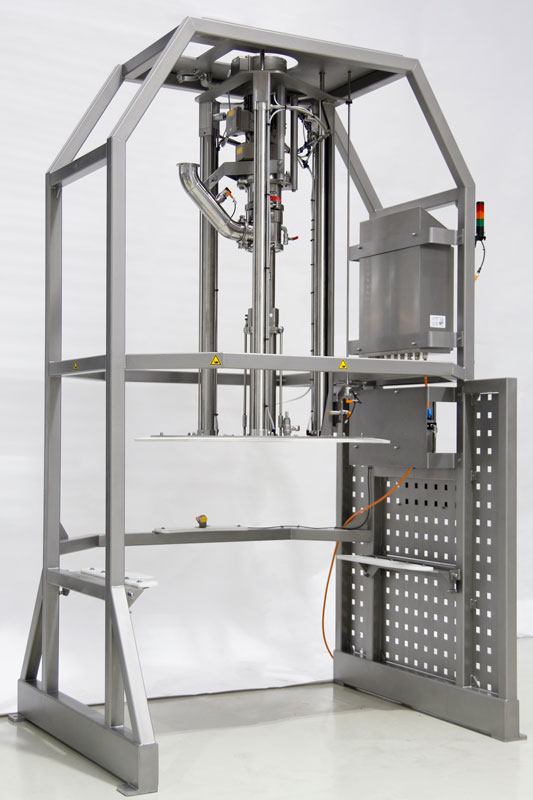
Picture 1: Barrel emptying system for a tank, for example for jam
The following example shows how this can be perfectly implemented: A German bakery uses the ViscoTec barrel emptying system ViscoMT-XL. This means that fillings for Danish pastry and puff pastry, as well as berlin doughnuts, are taken from 500 l tank and fed into the production line. The fillings have different viscosities: From liquid chocolate sauce to stiff vanilla cream to fillings containing pieces of up to 15 mm in size (such as cherry pastes). These sweet goods can therefore be filled with anything. One challenge facing process-reliable feeding is to supply the different fillings to the line very quickly and at the same time ensure the output quantity of pastries. Depending on the filling and the type of pastry, the demand and the feed speed can rise to 50 l / min.
The barrel emptying from ViscoTec can perfectly fulfill this criterion and supplies the line with sufficient filling material. The automated filling, directly from the tank into the hopper of the production line, facilitates the production process and the output of finished pastries is much higher. As a result, there is no downtime in the production line and the entire supply runs reliably. In addition, the user has the advantage that filling errors and wastage are avoided.
By implementing different sensors (e.g. level sensors in the tank or pressure sensors) the need to change the tank can be detected early and no production time is lost. Since the fillings are not exposed to their surroundings, there is no risk of contamination. At the end of a preparation phase in the tank, the fillings are immediately covered by the follower plate of the barrel emptying system and are ready to be filled into the pastry in a closed system.
Endless Piston Principle
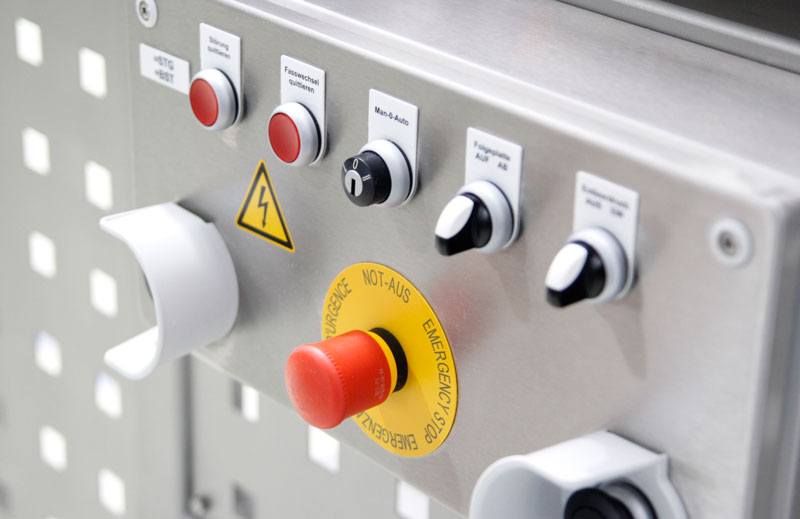
Picture 2: Control system for the emptying system
The progressive cavity pump forms the base of the barrel emptying systems from ViscoTec. It belongs to the group of rotary displacement pumps and is based on a volumetric pump technology. The operation is similar to an endless piston, which feeds the product from the suction side to the pressure side and thereby builds up a difference in pressure. The interaction of an eccentrically moving rotor and stator results in a feed and dosing characteristic that corresponds to that of an endlessly moving piston. Due to the dosing geometry, a constant volume is always fed proportionally to the rotation angle per revolution. The feed direction is reversible by reversing the direction of rotation. The volume is therefore clearly defined via the degrees of angle. This technique results in a pressure-stable, linear pump characteristic, which makes a clear statement about the ratio of revolution, time and flow rate. In turn, this leads to a guaranteed dosing accuracy at the pump outlet of 1 % (depending on the material), which in practice often falls below this percentage. Another benefit of this technology lies in the resulting feed chamber, whose volume remains constant over the course of the movement. This makes it possible to feed and fill solids-laden fluids and even chunky products. Even difficult, highly viscous liquids can be dosed reliably without pulsation, avoiding dosing errors or excessive stress on the material.
The Barrel Emptying of jam in practice
The extremely good suction capacity resulting from this technology is used in barrel emptying. In general, such a system consists of three essential components: Frame with lifting unit (1), emptying pump with follower plate (2) and control (3).

Picture 3: Emptying pump with follower plate
The pump – in this case the hygienic pump 2RD50 – is arranged vertically, the follower plate with wiper ring sits on the suction nozzle. All wetted parts are FDA compliant and food grade certified. ViscoTec pumps from the RD series (hygienic version) have excellent cleaning properties, are fully CIP and SIP capable and meet the highest hygiene standards. This pump type from ViscoTec holds the EHEDG (European Hygienic Engineering and Design Group) certificate.
During the process in which the various fillings are fed to the line, the pump continuously removes the pastes from the tank and feeds them via a hose line to the filling line. This creates a negative pressure in the container, which the follower plate “follows”. The inner wall of the container is wiped clean by the special sealing lip on the follower plate. By using this emptying principle of wiping the container, it is almost completely emptied, i.e. the remaining residual quantity is less than 1% and saves in both the cleaning effort and the pastes and fillings themselves, which would otherwise be discarded or manually emptied and fed into the line.
The emptying speed can be easily changed via the electric motor, by simply raising or lowering the motor speed. If, for example, the cycle time of the filling line needs to be increased, only the drive speed of the motor need be increased.
In addition, the system can be easily integrated into existing lines and manufacturing concepts. Even with lines where the masses and materials were previously fed manually, the system can be connected very easily: The tank emptying is operated completely autonomously, without interface to the existing filling line. A pressure sensor on the filling regulates the supply, which must not fall below a pre-parameterized minimum pressure. Should the pressure fall below this minimum, the emptying pump is automatically turned on until the necessary pressure is reached again. Another highlight is the sophisticated security concept, whereby the follower plate can only be raised and lowered by means of a two-hand operation. Positioning sensors monitoring the activity in the tank and protective guards guarantee that the operator cannot reach the moving parts of the system and injure himself. The position of the follower plate is detected continuously via a magneto-inductive displacement sensor. This ensures a shutdown of the pump when it reaches the bottom of the tank and prevents damage. To completely empty and clean the pump, it can be manually operated backwards.
The barrel removal from ViscoTec has a decisive advantage: Unlike barrel presses from other manufacturers, which sometimes apply up to 25 bar to the product and therefore destroy the material structure, ViscoTec barrel emptying system empties containers without using pressure. Due to the non-pressurized guidance of the follower plate, no material is squeezed sideways. And: No special safety precautions have to be taken with regard to the pressure resistance of the containers.
To summarize, it can be said that the barrel or tank emptying from ViscoTec has many advantages. In addition to easy handling, the hygienic emptying of the mixing tanks should be highlighted. ViscoTec emptying systems offer the perfect process-reliable solution for the filling of pastries and doughnuts.
More information about dosing and filling in food applications you can find here.
The post How does the jam get into a berlin doughnut? appeared first on ViscoTec Pumpen- u. Dosiertechnik GmbH.