When dosing highly viscous pharmaceutical products, high dosing pressures are often necessary for the precise dosing of very small quantities due to the nature of the process. The ability to displace fluid without pulsation while under high pressures is essential for applications such as supplying active ingredients into an extruder. The Pharma Dispenser from ViscoTec is ideal for these applications due to its excellent pressure stability even at high back pressures.
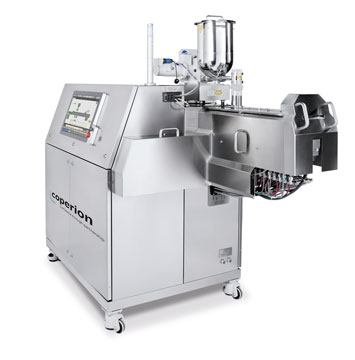
The ZSK 18 MEGAlab pharmaceutical extruder from Coperion K-Tron (Switzerland) LLC.
An example of one application is the production of various semi-solid materials in an extruder from Coperion, the technological market leader for continuous processes in the pharmaceutical industry. Coperion has unique know-how and many years of experience in the field of continuous extrusion processes. Since the beginnings of pharmaceutical extrusion, Coperion has been setting new standards for the continuous production of pharmaceutical products. This applies to laboratory-scale applications and product development as well as to continuous production systems. The extruder functions similarly to a very large progressive cavity pump. Various products are conveyed into the extruder and perfectly mixed. Dosing is continuous and practically pulsation-free. These are important prerequisites for high-quality end products.
Three ViscoTec dispensers are installed in the Coperion extruder, each of which continuously supplies different active ingredients with various viscosities. Two 3VPHD12 with 1.7 ml/rev dose 1.14 – 3.41 kg/h or 0.8 – 2.41 kg/h and one 3VPHD8 with 0.35 ml/rev dose 0.2 – 0.60 kg/h active ingredient. ViscoTec has impressed with its proven endless piston technology: “In our continuous manufacturing processes, the dosage quantity of the active ingredients must not vary. The smallest quantities must be dosed with perfect repeat accuracy and as pulsation-free as possible. With the ViscoTec dispensers, we were able to achieve exactly this precision. The easy disassembly and cleanability of the ViscoTec dispensers were also an important aspect for us,” says Bodo Reisert, Global Lead Engineer Food & Pharma at Coperion K-Tron (Switzerland) LLC.
Advantages of the ViscoTec Pharma Dispenser for continuous processes
- Continuous dosing: The endless piston technology enables a constant material supply of 0.18 ml per minute. In contrast to rotary piston pumps, there are no stoppages within the dosing process. And peristaltic pumps are strongly limited in pressure stability and often do not deliver pulsation-free dosing in this process environment.
- Hygienic Design: Easy to clean, no dead spaces. In order to meet the high cleaning requirements in pharmaceutical production, the Pharma Dispenser can be dismantled without tools. All product contact components can be cleaned manually, e.g. in ultrasonic baths or using CIP cleaning systems. Steam sterilization in autoclaves at max. 134 °C is also possible.
- GMP requirements for pharmaceutical processes: All metallic surfaces that come into contact with the product are made of high-quality stainless steel, are electro-polished and typically have a surface roughness of Ra < 0.8. This ensures safety against microbiological deposits and easy cleaning of all contaminated surfaces. All non-metallic wet parts are FDA-compliant elastomers. A comprehensive documentation for the validation of the dispenser is available. Inspection certificates 3.1 according to EN10204 are available for all stainless-steel wet parts. ViscoTec also provides IQ (Installation Qualification) and OQ (Function Qualification) support in the form of comprehensive qualification documentation as well as on-site support during commissioning.
- Pulsation-free: The interaction of an eccentrically moving rotor and a stator adapted to the application conditions results in a conveying and dosing characteristic that is equivalent to an endlessly moving piston. Due to the dosing geometry, a constant volume is always displaced per revolution in proportion to the angle of rotation. The volume is therefore clearly defined by the angular degrees. Due to the proven endless piston principle, volumetric dosing systems operate pulsation-free and gently on the product without reverse flows in the individual cavities. The ideal rolling behavior of the rotor results in extremely high repeat accuracy of the quantity and high precision dosing.
- Pressure stability: Linear, up to 20 bar with a constant dosing quantity. Dispensers, such as ViscoTec’s products, based on the endless piston principle, belong to the rotating positive displacement pumps. The stainless-steel rotor moves eccentrically in an elastomer stator. The interaction of rotor and stator creates cavities. These alternating cavities are sealed against each other. This results in a pressure-stable, linear pump characteristic curve of 0 – 20 bar.
- Linear, pulsation-free discharge volume: Directly proportional to the rotation of the drive unit. Endless piston technology results in a pressure-stable, linear pump characteristic curve. This in turn enables a clear assertion to be made about the ratio of rotation, time and flow rate. With ViscoTec dispensers, a constant volume can be dosed either according to time or according to the number of revolutions.
- This leads to a guaranteed dosing accuracy at the pump outlet of +/- 1 % (depending on the material to be dosed), which is often even less in practice.
The Pharma Dispenser is the ideal dosing technology for precise continuous small volume filling and pulsation-free conveying of medium to high viscosity pharmaceuticals or medical fluids.
Advantages of Continuous Dosing
Continuous production systems are compact and require less expensive floor space in clean rooms. In addition, the manufacturing process is achieved non-stop, in a fully automated plant, which considerably reduces the manufacturing time. The probability of human error and additional costs is also reduced by a shortened production time. In addition, end-to-end production enables flexible traceability, online process control and process recognition.
As in the above-mentioned application example, one of the problems to be solved in the implementation of continuous production of liquid to pasty medicinal products, is permanent and precise dosing. The progressive cavity technology already used as standard in conventional industries for pulsation-free dosing offers a real solution – transposed into Hygienic Design.
Here you can find further information about ViscoTec applications for the pharmaceutical industry.
The post Pharmaceutical Extrusion Process appeared first on ViscoTec Pumpen- u. Dosiertechnik GmbH.