ViscoTec’s positive displacement systems for 1-component and 2-component fluids and pastes are based on the “endless piston principle”. The two main components, rotor and stator are creating, geometrically constant, cavities that generate a constant flow rate without pulsation. This design allows many advantages when dispensing a variety of fluids such as UV adhesive, 2-component epoxy, thermal conductive pastes, silicones, shear sensitive fluids, solder pastes and fluids containing fillers, polyurethanes, and many more fluids.
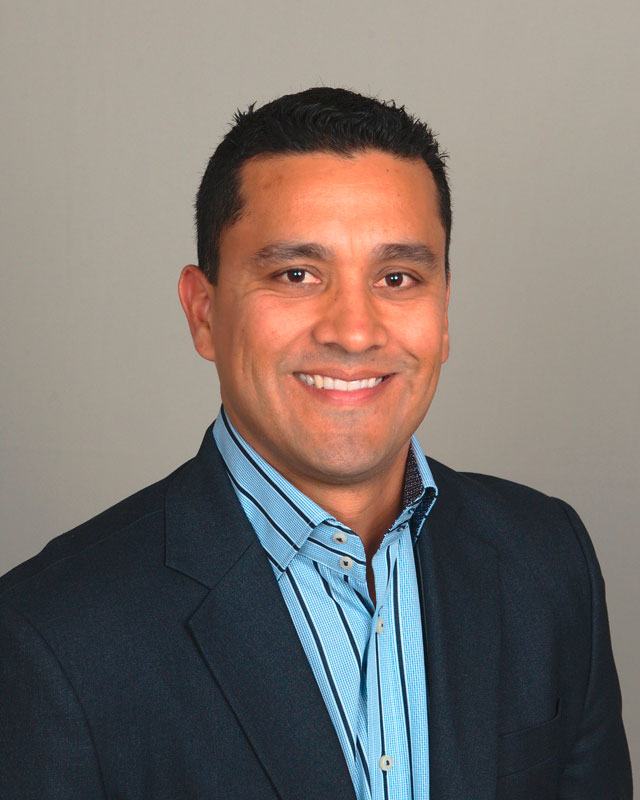
Dan Sotelo, Western Region Sales Manager at ViscoTec America Inc.
Dan Sotelo has been with ViscoTec America since 2016. He is responsible for growing and serving the customers in the Western region. Offering solutions from dispensing, emptying materials from a variety of containers, to treating the material such as degassing and agitation. In total he has been working in the fluid dispensing industry since 2007 – bringing solutions to manufacturing engineers to improve their fluid dispensing processes.
As an expert in dispensing technology he answers a few questions about high-precision dispensing of adhesive and about ViscoTec and its technology in particular.
Dan, in which branches is 1 & 2 component adhesive dispensing popular at the moment?
We cover a wide range of applications in industries such as Medical Device, Automotive, Electronics, Aerospace, Biotechnology, Food, Cosmetics, and 3D printing. Whenever or wherever it comes to manufacturers wanting to move away from manual to automated adhesive dispensing we are the perfect partner. Our preeflow dispensers have been popular due to their ability to dispense small amounts of material (even as small as 1 micro-liter with >99 % of repeat accuracy).
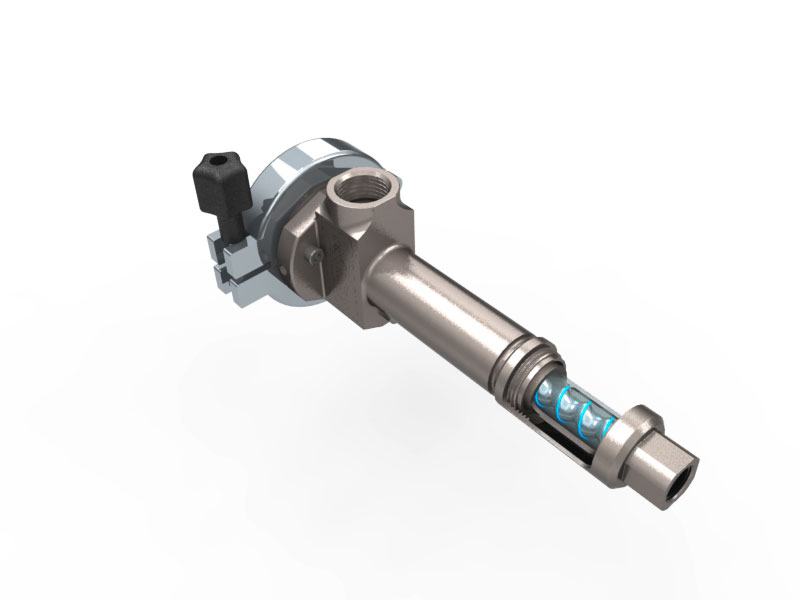
Progressive cavity pump technology: Each individual cavity delivers an exactly defined material volume and simultaneously serves as a sealing line in the direction of the pump, between inlet and outlet side.
What is the main issue in dispensing fluids and especially adhesives?
One of the main issues I see in fluid dispensing and therefore, of course, in adhesive dispensing processes have to do with materials changing: In viscosity, pressure fluctuations, or stringy materials that are hard to control after every dispensing cycle. This results in affecting repeatability of the quantity of material being dispensed and therefore can end up with scrap and material waste which can be eliminated with our progressive cavity technology.
We are also able to improve processes where 2-component materials need to be mixed and dispensed in small quantities. In many cases, these materials are dispensed with a manual gun or are either being hand mixed to fill a syringe and dispensed with a foot pedal dispenser. As you can imagine, this could be time consuming and can also result in uncontrolled amount of material being dispensed due to the short curing cycle. Our 2-component technology allows you to meter mix on-demand as needed and therefore eliminating waste.
Besides the advantages you already mentioned, why should somebody choose ViscoTec?
Manufacturers should choose ViscoTec technology because the 1- and 2-component dispensing systems are fully volumetric, and they can take advantage from the following benefits:
- Pressure stability
- Pulsation free
- Quantity and speed are directly proportional to each other
- Exact volume control
- Independent of varying viscosities
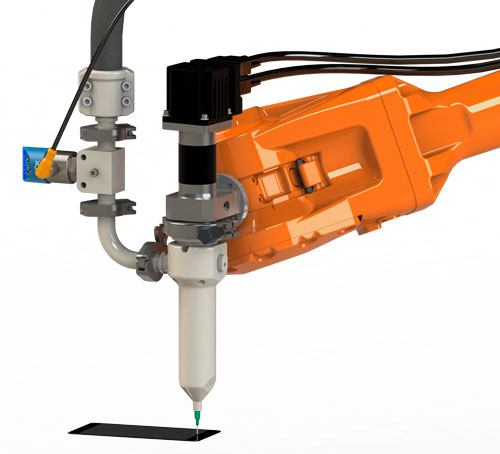
A ViscoTec metal-free dispenser mounted on a 6-axis robot arm dispenses adhesive – metal-free in the area in contact with the product.
And which solutions does ViscoTec offer? What is special about the ViscoTec products?
The solutions that ViscoTec offers range from systems to dispense 1-component and 2- component materials, to filling pumps, systems for emptying and degassing the material, as well as 3D printing heads – all from one source.
ViscoTec has an experienced and dedicated team to make sure you get the right solution for your application.
Which materials can ViscoTec handle best?
We are the specialist for demanding materials. Especially highly abrasive, gap fillers, solder pastes, flux agents, thermal pastes, shear-sensitive, compressible, and high viscosities of up to 7,000,000 mPas are our specialty. We always say: We start where others give up.
Here you can find all our 1- and 2-component dispensers – perfectly suitable for adhesives!
The post Improve your fluid dispensing process appeared first on ViscoTec Pumpen- u. Dosiertechnik GmbH.