flowscreen is a very rugged and compact device (with dimensions of 190 x 135 x 35 mm). The compact unit can be easily integrated into existing systems. It is suitable for various application fields. The analog input signals are presented by a special developed software on the 4.3“ TFT display. It creates a time/pressure graph based on the measured values in the form of an XY-Axis-graph.
Frequently the flowscreen is used in the dosing technology for process monitoring:
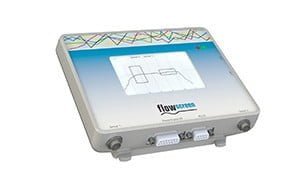
flowscreen process monitoring unit for flowplus16
A lot of factors are influencing the dosing quality a lot here: For example process fluctuations like unstable or pulsating flowrates, vibrant pressure variations, air pockets or homogeneity amendments can be monitored by flowscreen.
As signal generator the pressure sensor flowplus16 can be used for instance. But also sensors from other manufacturers can be used without any problems and perfectly coordinated with the flowscreen within a few seconds. The user can teach in evaluation criteria to ensure constant process parameters and reproducible series processes. Making these approaches can be managed application dependent; in addition adjustments can be performed intuitively by using the touchscreen.
Two different operating modes are the basis of process monitoring:
Whilst “range mode” is chosen, the complete range of a pressure gradient can be specified exactly. The “overpressure mode” on the other hand serves an individually configurable detection of peak loads. Regardless of the application, the sampling rate of the flowscreen is dynamically adapted in the range of 2Hz – 200Hz. The adaption depends on the measuring time from 0.1 seconds up to 40 minutes.
If defined evaluation criteria will be exceeded in relation to the process parameters during mass production, the errors will be signalized by a red fault LED and a message will appear on the screen. For extended communication the flowscreen can be connected to a master controller (PLC) additionally.
Deviations in the production process can be presented visually, thus an in-time accepted/non accepted judgment can be done from the system. Insufficient quality components can be removed immediately from the production line and/or the process parameters can be adapted. A cumulative error response can be realized in the flowscreen as well as a direct safety shut-down for the individual production plants.
For sustainable quality assurance of the respective application, the collected data can be logged via RS232 serial port for complete documentation. The flowscreen can help to reduce costs on the one side, and improve quality and customer satisfaction on the other side.
You can find further information about the fluidsensor flowplus and the matching evaluation unit flowscreen here.
The post Process monitoring in series manufacturing appeared first on ViscoTec Pumpen- u. Dosiertechnik GmbH.