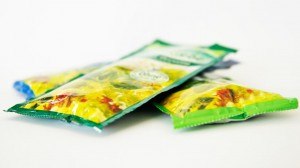
ViscoTec dosing technology application example: Filling of salad dressing in tubular bags
The fact that we use more and more products on the move has a clear impact on packaging development. It is hard to imagine everyday life without them: Food that is packed in sachets, stick packs or pouches. They reflect our fast-paced lifestyle and demographic change. Convenience food, such as ketchup and salad dressing, is popular due to its quick and portion-appropriate availability. But the trend towards smaller packaging sizes for cosmetic products, such as creams and shampoos, or the exact dosage for medicines and dietary supplements is also noticeable.
The challenges for manufacturers are growing with smaller packaging sizes. The dosing and filling of the different materials has to be carried out more precisely and evenly. For manufacturers who want to increase their productivity through maximum utilization of their packaging lines, a low reject rate is at least as important as high throughput times and performance. Special attention is paid to the bag filling process. To achieve a high production cycle, it is important to link the individual process steps as briefly and smoothly as possible. Precise and complex fine tuning of the dosing components is essential for this. Even the best sealing technology of the bag filling machines reaches its limits when the sealing surfaces are contaminated with product during filling or at the end of dosing and leakage occurs as a result. In addition to high material and energy consumption, significant costs can also arise in the form of production waste and consequently lead to lower productivity.
Complex cutting and closing devices and valves are often used to prevent dripping of thread pulling products. However, this additional equipment is subject to increased wear and tear and annoying maintenance times.
Less waste of food or cosmetics due to high-precision volumetric dosing technology
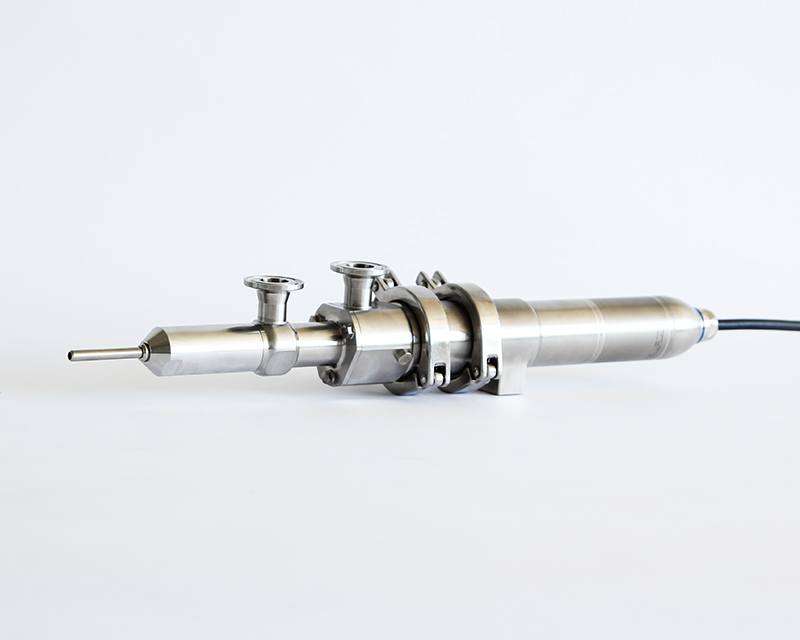
ViscoTec Hygienic Dispenser (VHD)
But no challenge for ViscoTec dosing systems: Smallest quantities are dosed or filled with a repeatability of more than 99 %. Thanks to the proven endless piston principle and its special rotor-stator geometry, no valve technology is required to prevent the medium from flowing out independently and uncontrolled. At the end of the dosing process, a programmable suck-back takes place, which is adapted to the product and ensures drip and thread-free filling. The individually controllable dosing units from ViscoTec guarantee hermetically sealed, reliable sealing seams for all product characteristics thanks to the sophisticated progressive cavity pump technology and thus support product quality and compliance with safety standards.
Your advantages with ViscoTec dosing and filling technology:
- Filling with a repeatability of 99 %
- Maximum protection of the products through low-shear and pulsation-free continuous conveyance
- No dripping due to adjustable + programmable suck-back
- Compliance with the guidelines: EHEDG, FDA, 3.1, GMP-compliant design
- Designed for optimum cleaning results at CIP/SIP
A dosing and filling pump was developed especially for small quantities in the food, cosmetics and pharmaceutical sectors. It meets the highest hygienic requirements and can also carry out reliable, high-precision and reproducible dosing for process dosing and filling systems. In order to meet the high cleaning requirements, the dispensers can be dismantled without tools in a few easy steps, but also especially for automated cleaning without disassembly, ViscoTec dispensers of the VHD series are optimized for best results with a CIP / SIP.
VHD dispensers convince:
- Less rejects due to sealed seams
- Highest precision even with smallest package sizes
- Independent of viscosity, temperature and density
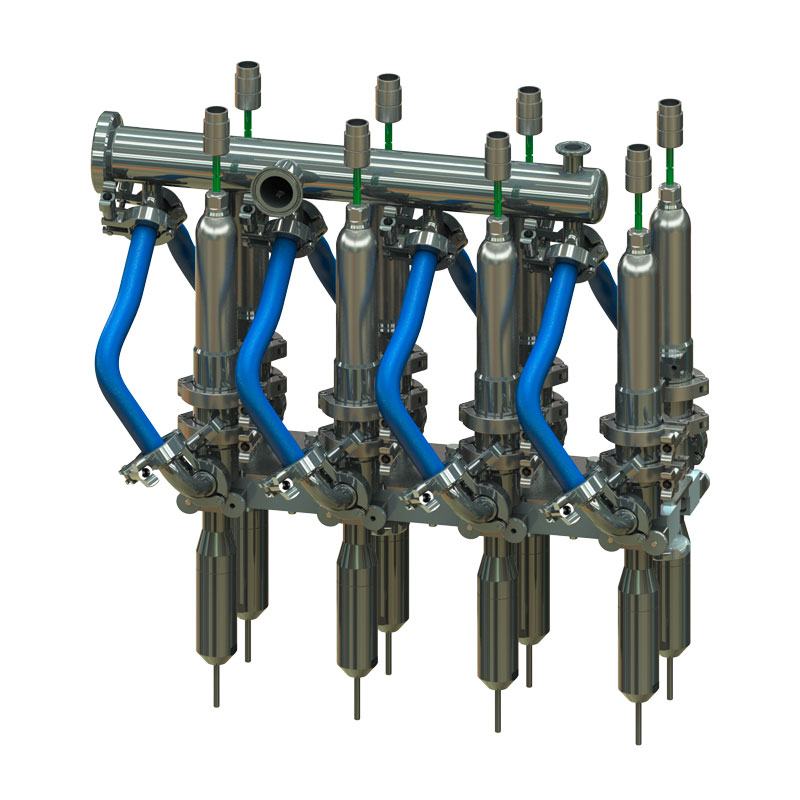
ViscoTec multiple dosing for low to high viscosity foodstuffs and cosmetics
The Hygienic Dispenser (VHD) is perfectly suited for filling highly viscous, abrasive liquids or pastes. Due to the small and very precise dosing quantities, individual products or even very small batches can be processed.
ViscoTec offers ideal dosing and filling systems for the safe, non-destructive and high-precision dosing of even the most difficult liquids. Chocolate, sugar mass, marinades, fruit fillings and spreads are just some of the products that can be filled flexibly with just one system. Customers trust ViscoTec’s experience, process know-how and worldwide service and support. This gives them the best and perfect solution for their applications.
The post Less waste due to “clean” filling appeared first on ViscoTec Pumpen- u. Dosiertechnik GmbH.